I have just such a room, a dining room, that has high traffic and is also used as a temporary workspace. It has 2 entrances, one from the kitchen and one from the lounge, with the 2 sets of doors being closed together. One of the doorways has a double door that really protrudes into the room. One of the double doors is always clattering into the door of the kitchen and blocking the walkway space into the room.
The solution was to make the double doors from the lounge into bifolds thus tucking the doors out of the way and stopping them from clashing with the kitchen door while freeing up walkway space around the door area.
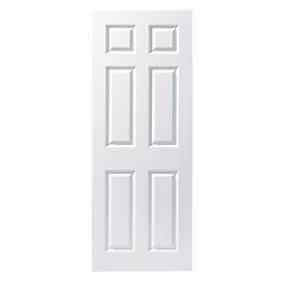
My initial search for 6-panel doors that came as readymade bifolds revealed only that they came as part of a kit where there was a track that would go along the header of the door in which the bifolded doors would run. The logic behind this was that the track was needed to support the doors when closed and keep them straight in the doorframe. This meant the doors in the kit were 30 or 40 millimetres shorter due to the track mechanism than I needed. I was planning to use thumb-turned rack bolts at the top and bottom of the door to hold the doors shut so I wanted full height doors.
The only option was to take 2 standard hollow 6-panel doors and turn them into a bifold door.
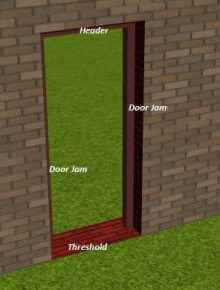
The doors were slightly too big for the opening so a line was scribed along the top with the doors being parallel to the jam on the hinge side giving the door a couple of millimetres clearance between the door and the header when cut. If the threshold of the door is not parallel with the bottom of the door then scribe a line on the bottom of the door as well. Make sure that timber removed from the top and bottom of the door leaves a gap above and below the door of a couple of millimeters. The timber was carefully removed using a fine 60 tooth bladed circular saw.
The doors were cut down the centre of the panels using the circular saw. The doors were clamped on top of 2 workbenches. Cutting the doors in half revealed the hollow insides of the doors which are filled with thin cardboard. The cardboard was pushed in to allow timber battens that were planed to be 27mm thick and 36mm wide to be glued in the gap and clamped.
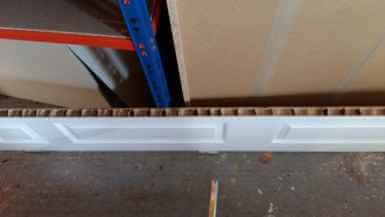
The doors were cut down the centre of the panels using the circular saw. The doors were clamped on top of 2 workbenches. Cutting the doors in half revealed the hollow insides of the doors which are filled with thin cardboard. The cardboard was pushed in to allow timber battens that were planed to be 27mm thick and 36mm wide to be glued in the gap and clamped.
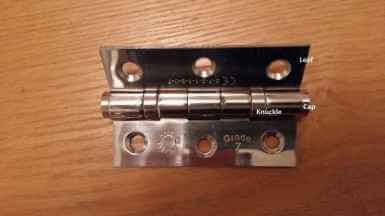
The doors were cut down the centre of the panels using the circular saw. The doors were clamped on top of 2 workbenches. Cutting the doors in half revealed the hollow insides of the doors which are filled with thin cardboard. The cardboard was pushed in to allow timber battens that were planed to be 27mm thick and 36mm wide to be glued in the gap and clamped.
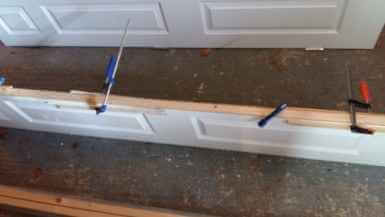
Clamp the 2 doors together and mark the position of the hinges that join the 2 doors together. Then using the router chop out the housings for the hinges. Fit the hinges to the 2 doors so that they join together and then hang the door into the frame. Repeat these steps for the other door. Adjust the depth of the hinges to allow the minimum gap when closed.

Clamp the 2 doors together and mark the position of the hinges that join the 2 doors together. Then using the router chop out the housings for the hinges. Fit the hinges to the 2 doors so that they join together and then hang the door into the frame. Repeat these steps for the other door. Adjust the depth of the hinges to allow the minimum gap when closed.
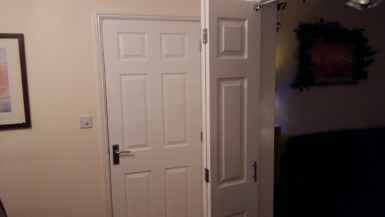